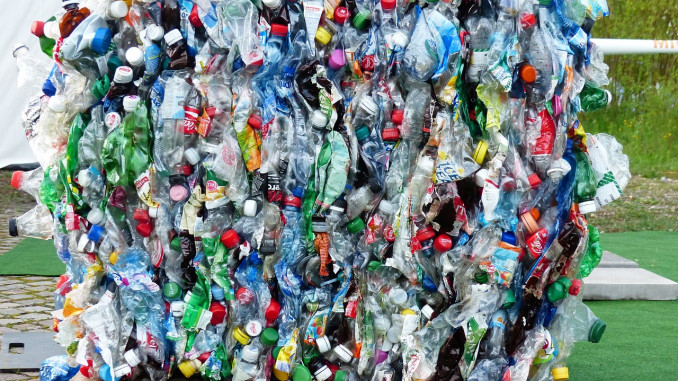
Maria Kanellopoulou
International Baccalaureate Diploma Program, Pinewood, The American International School
mkanellopoulou@pinewood-school.gr
Abstract
With the growing production of plastics, many concerns have been raised about their possible effects and impact on the environment. Only 9% of all used plastic is recycled, however, plastic represents a versatile class of material and they are part of life and irreplaceable in many applications. In this study, raw materials are used as single-use plastics and a plastic injection machine to re-shape them into a product that can be used for any purpose. To create a quality product, the physical properties of the re-shaped plastics are tested. In particular, commonly used plastics that belong to polyolefins and biopolymers were used. More specifically, two different types of polypropylene were selected which are commonly used in packaging, food containers and pipe applications. Moreover, polylactic acid which is a biopolymer that has many medical and pharmaceutical applications was used. Different thermal processing temperatures, in the range between 210 oC to 280 oC, have been investigated as well as the recycled extrusion cycle (how many times the plastics can be recycled without using their performance properties (expressed as angle of depression). Plastic materials might lose some of their performance properties and the mechanical strength when the number of extrusion cycles increases, however, it has been concluded that plastic materials tend to regain their original shape after having been exposed to mechanical pressure applied by an object weighing 300g.
Keywords: plastic recycling, injection molding, polyolefins, biopolymers, sustainability
Introduction
Plastic materials, also known as polymers, represent an indispensable part of modern society. It is well known that plastics on one hand make our lives easier by bringing great convenience in a large number of applications, on the other hand, render a series of post-treatment challenges. Plastics are low-cost, light weight, flexible, corrosion resistant materials that make them almost irreplaceable in society, however, all this convenience comes at the expense of increasing amounts of plastic consumption (Usman et al, 2023). The fast growth of plastic production indicates that they are playing a more important role in our human life now than ever. However, the massive use of plastic also results in a great challenge of plastic disposal. Since plastics exhibit very low decomposition rate in the environment, they would exist in the environment for many years if left untreated (Kalali, 2023, Plastics, the fast facts, 2023). As a matter of fact, it will cause severe pollution issues, which are difficult to deal with.
In recent years, plastics recycling is receiving more attention, and consequently, many strategies have been proposed and applied in the treatment of plastics waste (e.g., pyrolysis, gasification, chemolysis, mechanical recycling, biological recycling, see Figure 1). However, the current efforts in dealing with the plastic waste may not be enough. Until 2017, the total plastic production has reached a total of 9200 million metric tons, however, only about 6.0% (550 million metric tons) has been recycled, and more than half ends up as plastic waste, see Figure 2 (Numanuddin et al. 2023, Marine Plastic Pollution, 2023, Plastics, the fast facts, 2023).
Figure 1: Schematic representation of the waste plastic management
Figure 2: Distribution of plastic waste treatment globally
In the meantime, another challenge is the emission of greenhouse gasses due to our recycled plastic waste. In 2019, the emission of green-house gas from the plastic lifecycle worldwide was reported to be 0.86 million tons (Mt) of carbon dioxide (equivalent), and it may reach 2.80 Mt of carbon dioxide in 2050 (Usman et al. 2023, Numanuddin et al. 2023, Plastics, the fast facts, 2023). However, the use of plastics is inevitable, and this particular class of materials has played an instrumental role in the development and advancement of society. It has to be highlighted that to this date, there are no commercially feasible alternatives to match the performance properties of plastics showing that the development and commercial application of alternative materials is slow or limited.
However, based on the latest technological developments, the mechanical recycling technology, represents the most promising and rapidly developing polymer recycling technology that has shown the greatest potential to efficiently (fast and with low cost) separate plastic waste and use it to further process it via well-known processing techniques that are used for the so-called virgin plastic (e.g., injection molding, casting, etc.) to produce various products. The present study deals with the formulation of plastic items like a ruler or hexagonal tiles using different types of recycling plastics (two different types of polypropylene, PP and polylactic acid, PLA) by employing a well-known processing technique, namely injection molding. In particular, the selected plastic material was collected by mechanical recycling, then it was reduced in size to produce polymer flakes (via a size reduction process, known as shredding), and it was further processed using a lab-scale injection molded unit to produce the final product. The effect of processing temperature and the number of cycles were investigated on the produced material performance to assess the possibility to re-use already processed recycling plastic.
Materials and Methods
The experimental investigation has been carried out in the lab (see Figure 3a) that was well equipped with the shredder, the injection molding unit, the oven and other auxiliaries.
Figure 3a: Overview of the lab- Plastic Garage at Linz, sponsored by Borealis Polyolefine GmbH
Figure 3b: Personal protective equipment and molds used in the experiments
Therefore, special attention was placed on safety in operational laboratories and, thus, personal protective equipment has been employed (see Figure 3b), i.e., safety glasses and gloves (Lab safety guide, 2024, Hibbard, 2021). Recycled polymers (i.e., polypropylene and polylactic acid) have been collected (single feedstock stream) after being processed (cleaning and shredding) as part of a mechanical recycling process. A photo showing the lab-scale shredder is illustrated in Figure 4.
Figure 4: Small-scale shredder used to reduce the size of the plastics
In particular, the hopper opening of the shredder was filled with plastic to be recycled and then the crank started operating counterclockwise. Depending on the plastic type, more or less strength is required. As the shredding process proceeds, plastic parts are slowly fed, until a steady state. is reached. However, in some cases, the shredder was blocked, so in that case, the crank was turned in the opposite direction. To achieve the desired result (fine shredding) it is recommended to repeat the process to properly reduce the size of the flakes which in turn is beneficial for the injection molding unit. As an example, it was found that flakes having a size below 10 mm are suitable for the injection molding unit.
Once the shredding process of each polymer is finished, intensive cleaning was carried out to avoid contamination of the polymeric samples. As part of the cleaning process, it is suggested to unscrew the hopper opening to get access to the blades and clean them properly (i.e., use of brush and compressed air). The process above was repeated for each type of polymer and a container was placed below the shredder to collect the polymer material.
The shredded recycled plastic was further used in the small-scale injection molding unit (see Figure 5) in which two different molds were used (hexagonal tiles and rulers).
Figure 5: Lab-scale injection molding unit
The injection molding unit depicted in Figure 5 was employed to produce the articles. Regarding the operation of the unit, it was set up to the selected operating temperature that takes around 10 minutes to be reached. After that, the plunger (1) is brought to the upper position by turning the handwheel (3). Then the hopper (4) is filled with the plastic flakes making sure that the plastic gets into the injection barrel (6). Subsequently, the plastic is compressed in the pipe by turning the plunger down. The plastic is left for about 10 mins to melt. It was found very useful to clamp a piece of wood between the nozzle (8) and the clamping table (10) to prevent the plastic from running out of the barrel. While the polymer material melts the molds are set up by placing them on the side table (7). Once the polymer melting process is finished, the mold is placed in the nozzle and the spring clamp system (9) is properly set up so that the mold is adjusted (i.e., the mold is adjusted between the nozzle (8) and the table (10). The injection process starts by filling the mold by turning the handwheel sharply. The final step includes the de-moulding process (opening of the mold and removing the shaped polymer, i.e., hexagonal tile or ruler). The process has been repeated for various operating temperatures (i.e., to find the optimum temperature) and the various polymer types.
The procedure for the testing comprises the following steps: i) using a clamp to hold the ruler which is made from the recycled material at the 4 cm mark, ii) place a string at the 14 cm mark with a weight of 300g, iii) measure the cm of the bent in the recycled plastic ruler by using the meter placed vertically taped on the wall, iv) calculate the angle of the bend (also termed as degree or angle of depression) in the ruler using geometry.
Results
The processed polymeric materials look the same after all extrusion cycles; a few specimens were not straight due to insufficient cooling time after they came out of the mold. It is well known that when the polymer material is hot it tends to change shape; this is the reason that some of the produced items are slightly bent. It was found that the type of plastic that had the best performance was the polypropylene 1. This suggests that it can be used and recycled many times. Figure 6 shows the effect of the type of plastic and the number of extrusion cycles on the angle of the bend (i.e., degree of depression) of the recycled ruler.
Figure 6: Effect of the type of plastic and the number of extrusion cycles on the angle of the bend of the recycled ruler.
Figure 7: Representative pictures of the rulers made at each extrusion cycle (one cycle to three cycles from the right photo to the left. The gray ruler is made by polypropylene type 1, the white ruler is made by polypropylene type 2 and the blue ruler is made by polylactic acid).
In addition, various operating temperatures (i.e., from 210 oC to 280 oC) were used and the optimal ones for each processed polymer are shown in Table 1.
Polymer Type | Processing Temperature (oC) |
PP1 |
225 |
PP2 |
230 |
PLA |
255 |
Table 1: Optimum operating temperatures for the various polymer types.
It was found that when the recycled polymers were processed during the injection molding at temperatures below the optimal ones, the shape of the mold was not the desired one, see Figure 8. This is attributed to the melting temperatures of the virgin polymer (A Practical Approach to Rheology and Rheometry, Gebhard Schramm, 1994) as well as to the homogeneity of the samples.
Figure 8: Effect of low process temperature on injection molding quality.
Moreover, the recycled extrusion cycle (how many times the plastics can be recycled without using their performance property was studied. Thus, the produced articles were re-shredded, melted and injection molded. It was found out that after the second cycle, small deterioration of the mechanical properties was observed.
Overall the durability of the plastic does not change that much this means that we can process plastics without losing the key performance properties. We were only able to test the strength of the ruler with a 300g weight plate but even if the ruler bent it regained its original shape. This shows that we can process plastics that are used in everyday applications.
Conclusions
In the present study, recycled polymer collected from the mechanical recycling process was formulated using a small scale injection molding unit to produce hexagonal tiles and rulers. The effect of processing temperature and the number of cycles were investigated on the produced material performance to assess whether already processed recycling plastic can be re-used. It was found out that the optimum operating temperature for the PP polymers was 230 oC, while the corresponding one for the PLA was 255 oC, that is correlated with the melting point of the virgin polymers (i.e., 160 oC for PP and 175 oC for PLA). Moreover, the recycled material extrusion cycle has been investigated and concluded that after the second extrusion cycle of the recycled polymer, its mechanical properties (indirectly correlated to the angle of depression of the ruler) are slightly changed. Moreover, the strength and durability of the plastic materials that are tested were not significantly changed even after the third extrusion cycle, thus, they can be re-used as recycled feedstock.
Acknowledgements
The author would like to deeply acknowledge and thank Borealis Polyolefine GmbH and the Plastic Garage in Linz in Austria (https://www.plasticgarage4020.at/ , https://grandgarage.eu/) for the ample support and for providing full access to the experimental facilities. Special thanks to Mr. Ammar Makic and Dr. Johannes Fellner for their continuous support, guidance and facilitation during the study as well as for providing the raw material and special pieces of training to lab operations and to the use of the equipment and the experimental units.
References
- Usman Salahuddin, Jiyu Sun, Chunxiang Zhu, Mudi Wu, Binchao Zhao, and Pu-Xian Gao, Adv. Sustainable Syst. 2023, 7, 2200471, Plastic Recycling: A Review on Life Cycle, Methods, Misconceptions, and Techno-Economic Analysis.
- Numanuddin Azad, Deblina Dutta, Bholu Ram Yadav, Sunil Kumar, Rahul Tiwar, Science of the Total Environment, 2023, 881, 163433, A critical review and future perspective of plastic waste recycling
- Ehsan Naderi Kalali, Saeid Lotfian, Marjan Entezar Shabestari, Saber Khayatzadeh, Chengshou Zhao, and Hamed Yazdani Nezhad, Current Opinion in Green and Sustainable Chemistry, 2023, 40:100763, A critical review of the current progress of plastic waste recycling technology in structural material.
- Plastics – the Fast Facts.” Plastics Europe, 2023, plasticseurope.org/knowledge-hub/plastics-the-fast-facts-2023
- “Marine Plastic Pollution.” IUCN, 2023, www.iucn.org/resources/issues-brief/marine-plastic-pollution#:~:text=If%20discarded%20improperly%2C%20plastic%20waste,waters%20to%20deep%2Dsea%20sediments.
- “Lab Safety Guide: Environmental Health and Safety.” Lab Safety Guide | Environmental Health and Safety, ehs.stonybrook.edu/programs/laboratory-safety/lab-safety-guide#:~:text=Never%20eat%2C%20drink%2C%20chew%20gum,coats%20before%20leaving%20the%20lab, accessed 25 Feb. 2024.
- Troy Hibbard, “How to Stay Organized in the Lab.” Bitesize Bio, 8 Oct. 2021, bitesizebio.com/19202/how-to-stay-organized-in-the-lab/.
- A Practical Approach to Rheology and Rheometry, Gebhard Schramm, 1994, 2nd edition, publisher Gebrueder Haake.